FRP Pultruded Grating Fire Retardant/Chemical Resistant
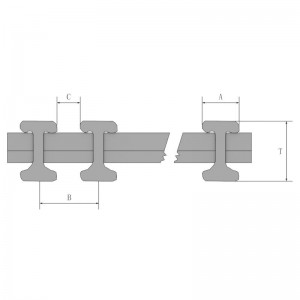
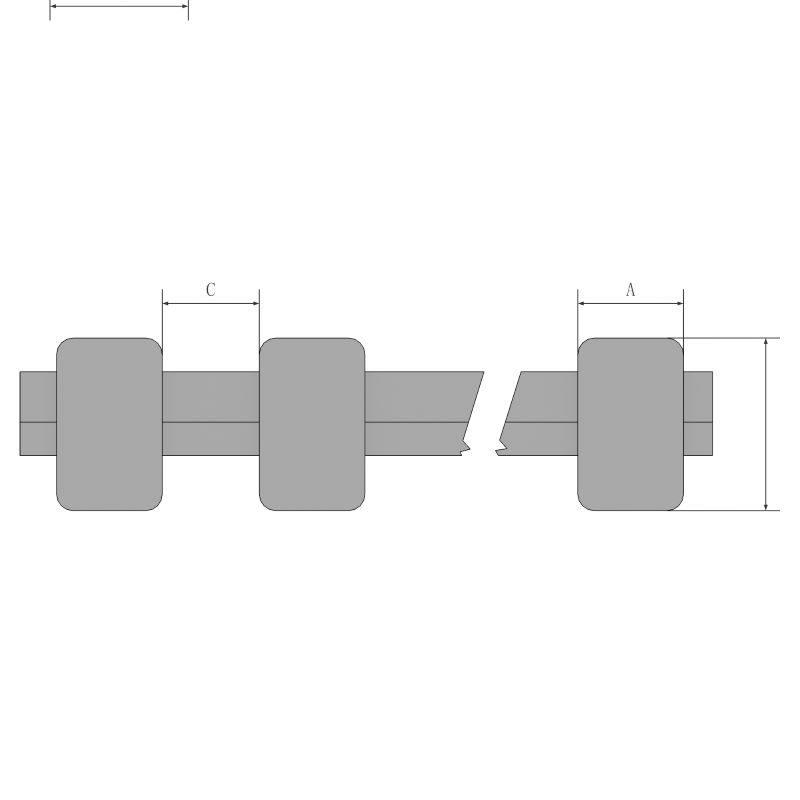
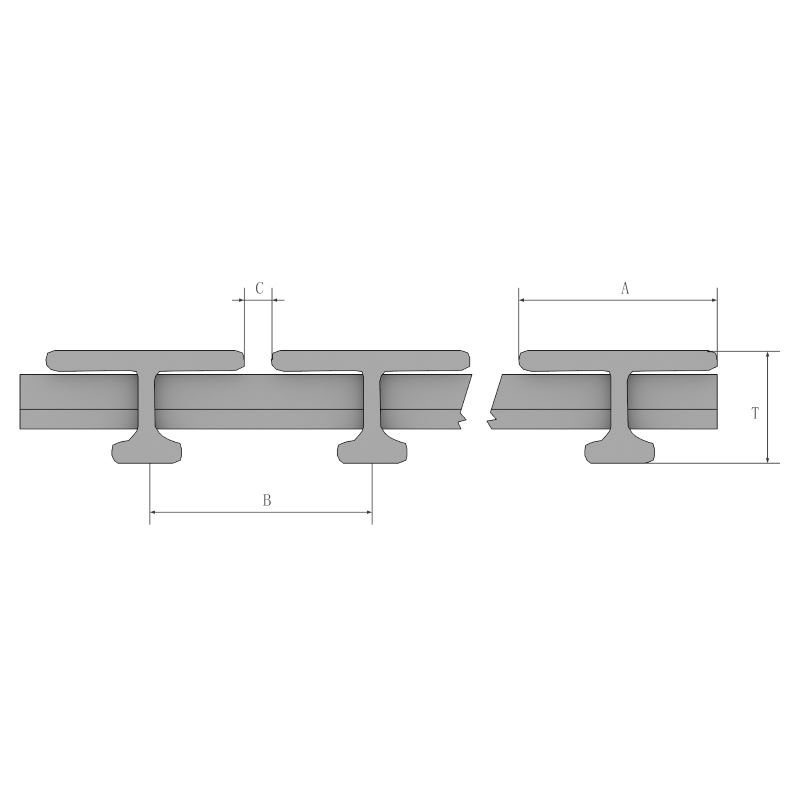
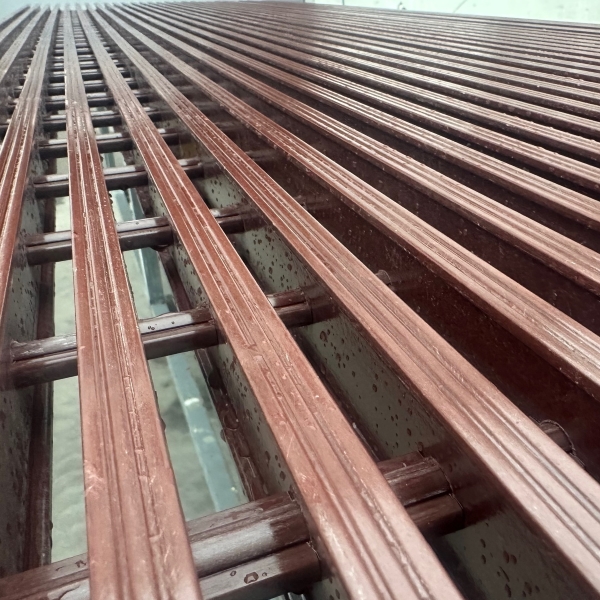
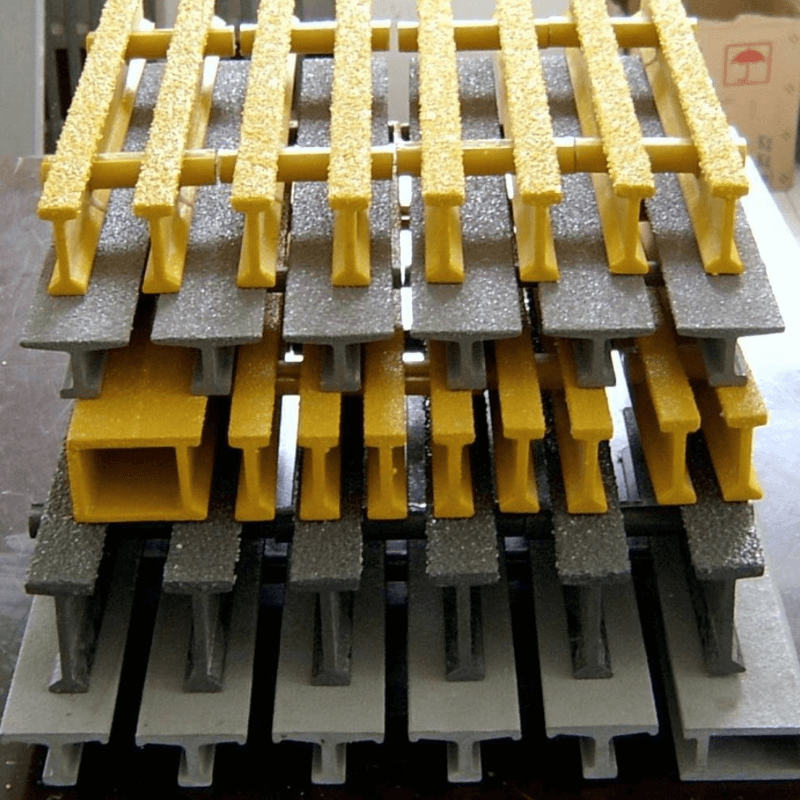
Parts of molded FRP Pultruded grating exhibitions :
I-5010 | 50 | 15 | 25 | 10 | 40 | 28.5 |
I-5015 | 50 | 15 | 30 | 15 | 50 | 24.2 |
I-5023 | 50 | 15 | 38 | 23 | 60 | 20.1 |
T-2510 | 25 | 38 | 43.4 | 5.4 | 12 | 15.6 |
T-2515 | 25 | 38 | 50.8 | 9.5 | 18 | 13.9 |
T-2520 | 25 | 38 | 50.8 | 12.7 | 25 | 13.6 |
T-2530 | 25 | 38 | 61 | 19.7 | 33 | 11.2 |
T-3810 | 38 | 38 | 43.3 | 5.2 | 12 | 19.6 |
T-3815 | 38 | 38 | 50.8 | 12.7 | 25 | 16.7 |
T-3820 | 38 | 38 | 61 | 23 | 38 | 14.3 |
T-5010 | 50 | 25.4 | 38.1 | 12.7 | 33 | 21.8 |
T-5015 | 50 | 25.4 | 50.8 | 25.4 | 50 | 17.4 |
H-5010 | 50 | 15 | 10 | 10 | 40 | 63 |
H-5015 | 50 | 15 | 15 | 15 | 50 | 52.3 |
H-5020 | 50 | 15 | 23 | 23 | 60 | 43.6 |
Pultruded Grating type | Height(mm) | Top edge width(mm) | Space between(mm) | Clearance width(mm) | Open area(%) | Estimated weight Kg/㎡ |
I-2510 |
25 | 15 | 25 | 10 | 40 | 17.8 |
I-2515 | 25 | 15 | 30 | 15 | 50 | 15.2 |
I-2523 | 25 | 15 | 38 | 23 | 60 | 12.2 |
I-3810 | 38 | 15 | 25 | 10 | 40 | 22 |
I-3815 | 38 | 15 | 30 | 15 | 50 | 19.1 |
I-3823 | 38 | 15 | 38 | 23 | 60 | 16.2 |
I-3010 | 30 | 15 | 25 | 10 | 40 | 19.1 |
I-3015 | 30 | 15 | 30 | 15 | 50 | 16.1 |
I-3023 | 30 | 15 | 38 | 23 | 60 | 13.1 |
FRP Resins Systems Choices:
Resins options guide:
Resin Type | Resin Option | Properties | Chemmical Resistance | Fire Retardant(ASTM E84) | Products | Bespoke Colors | Max ℃ Temp |
Type P | Phenolic | Low Smoke and Superior Fire Resistance | Very Good | Class 1, 5 or less | Molded and Pultruded | Bespoke Colors | 150℃ |
Type V | Vinyl Ester | Superior Corrosion Resistance and Fire Retardant | Excellent | Class 1, 25 or less | Molded and Pultruded | Bespoke Colors | 95℃ |
Type I | Isophthalic polyester | Industrial Grade Corrosion Resistance and Fire Retardant | Very Good | Class 1, 25 or less | Molded and Pultruded | Bespoke Colors | 85℃ |
Type O | Ortho | Moderate Corrosion Resistance and Fire Retardant | Normal | Class 1, 25 or less | Molded and Pultruded | Bespoke Colors | 85℃ |
Type F | Isophthalic polyester | Food Grade Corrosion Resistance and Fire Retardant | Very Good | Class 2, 75 or less | Molded | Brown | 85℃ |
Type E | Epoxy | Excellent corrosion resistance and fire retardant | Excellent | Class 1, 25 or less | Pultruded | Bespoke Colors | 180℃ |
Bespoke ColorsAccording to the different environments and applications, chosen different resins, we also could provide some advices!
Phenolic resin (Type P): The best choice for applications requiring max fire retardant and low smoke emissions such as oil refineries, steel factories, and pier decks.
Vinyl Ester (Type V): withstand the strict chemical environments used for chemical, waste treatment, and foundry plants.
Isophthalic resin (Type I): A nice choice for applications where chemical splashes and spills are a common occurrence.
Food Grade Isophthalic resin (Type F): Ideally suitable for food and beverage industry factories which are exposed to strict clean environments.
General Purpose Orthothphalic resin (Type O): economic alternatives to vinyl ester and isophthalic resins products.
Epoxy Resin(Type E):offer very high mechanical properties and fatigue resistance, taking the advantages of other resins. Mold costs are similar to PE and VE, but material costs are higher.
Products capacities test laboratory:
The meticulous experimental equipment for FRP pultruded profiles and FRP molded gratings ,such as flexural tests,tensile tests,compression tests, and destructive tests. According to customers’ requirements,we will conduct performances & capacities tests on FRP products ,keeping the records to guarantee the quality stability for long-term.meanwhile, We are always researching & developing innovative products with testing the reliability of FRP product performance. We can ensure that the quality can satisfy customers’ requirements stably to avoid unnecessary after-sales problems.
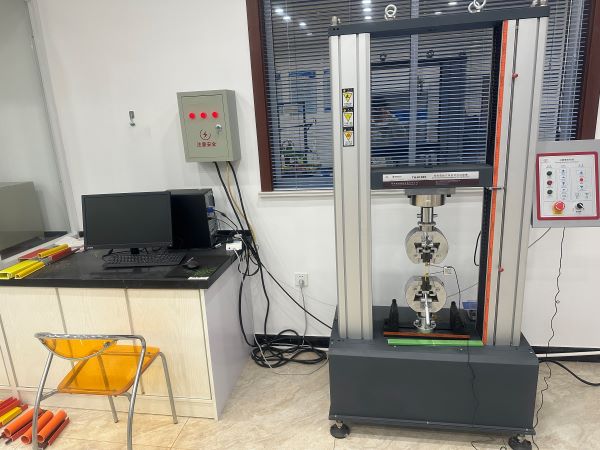
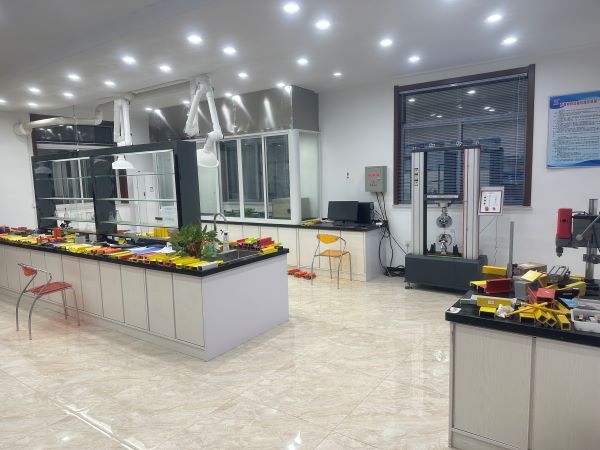
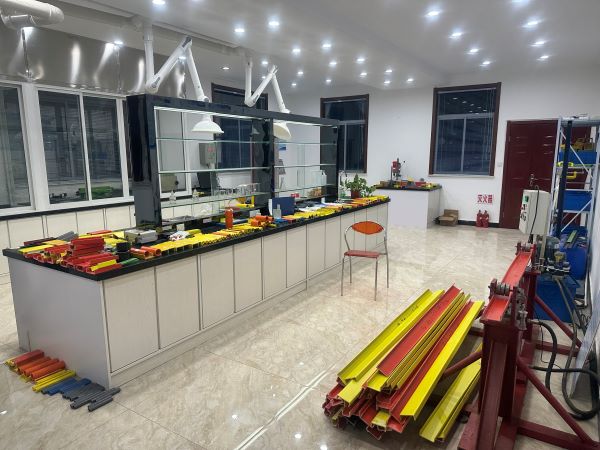
SINOGRATES@FRP Pultrusion Grating
Pultrusion process is a manufacturing process for producing continuous lengths of reinforced polymer structural profiles with constant cross-sections. Raw materials are a liquid resin mixture ( resins,fillers and specialized additives) and flexible textile reinforcing fiberglass rovings . The process involves pulling these raw materials (rather than pushing, as is the case in extrusion) through a heated steel forming die using a continuous pulling device.
The reinforced materials are in continuous forms such as rolls of fiberglass mats and doffs of fiberglass rovings. As the reinforcements are saturated with the resins mixture ("wet-out") in the resin bath and pulled through the die, the gelation, or hardening, of the resin is initiated by the heat from the die and a rigid, cured profile is formed that corresponds to the shape of the die.
FRP Pultrusion grating comes in three categories: I-Shape bars, T-Shape bars, and High-Load bars for Heavy-Duty Applications.
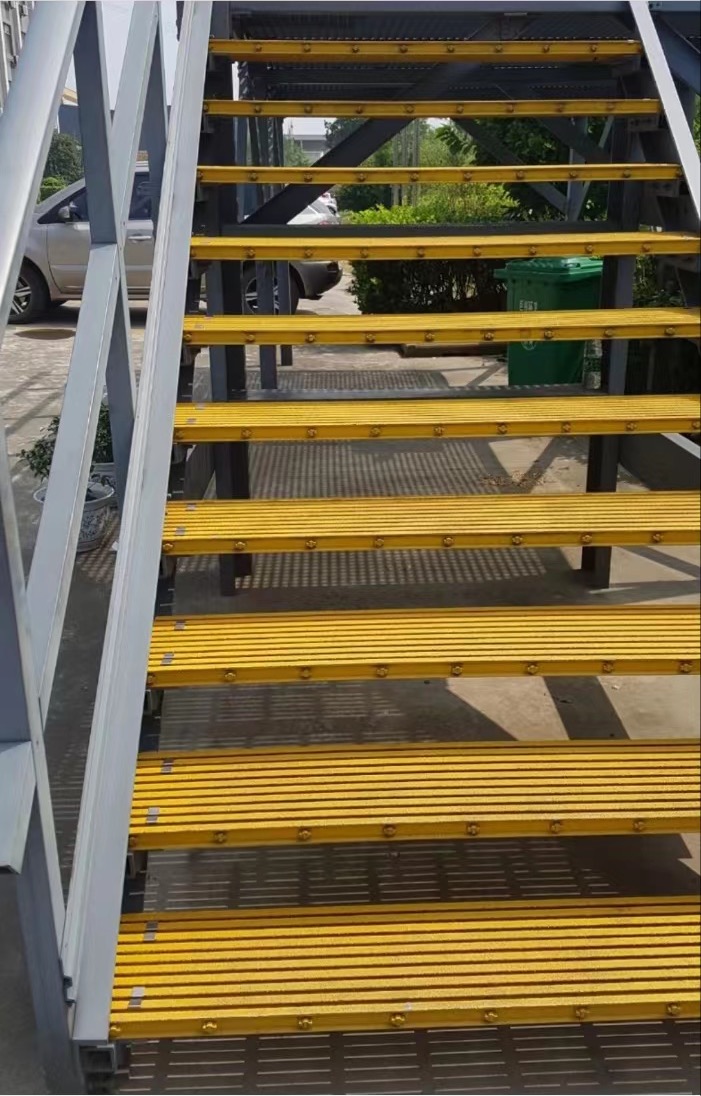